Two minutes can change the future of your organization.
See how Process Optimizer is changing the way organizations succeed.
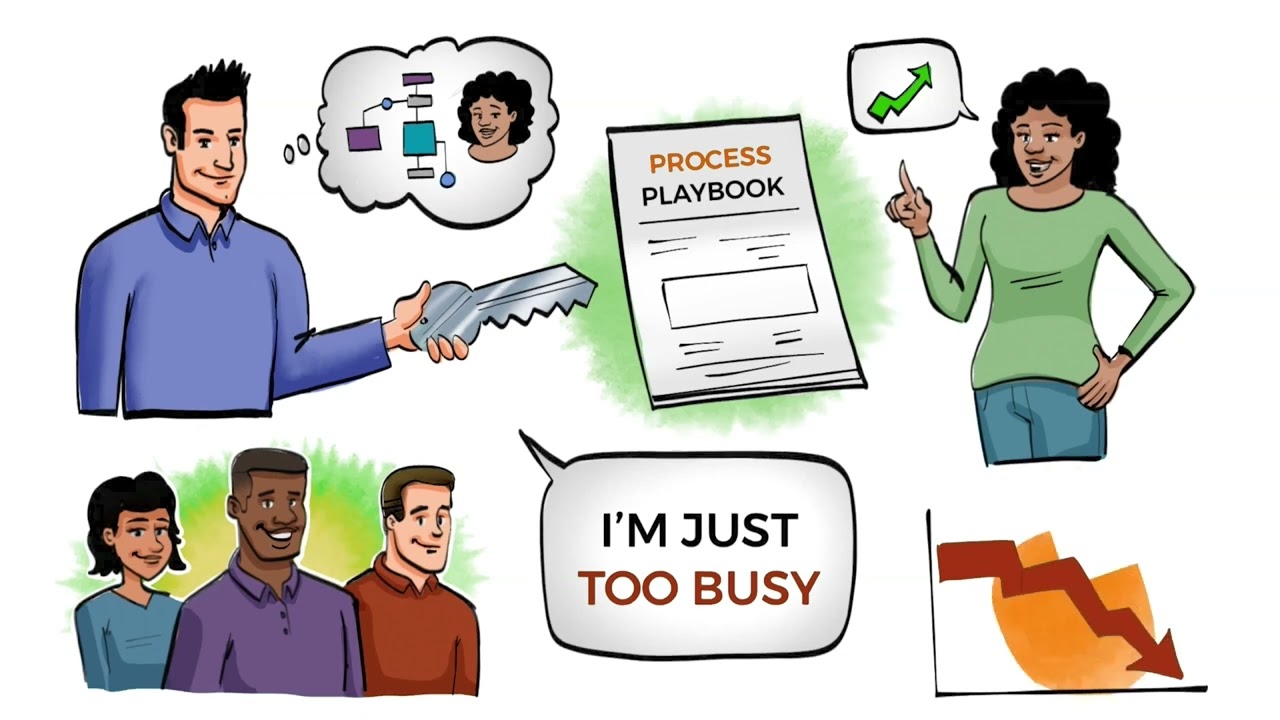
ARE YOU SOLVING THE SAME ISSUES AGAIN AND AGAIN?
The majority of issues entrepreneurial organizations face are rooted in either people or process. And if your processes have not been defined, optimized, documented and delegated, you aren’t giving your people one of the most important tools they need to do their jobs well — your Business Playbook.
GO FROM CHAOS TO CONSISTENCY
Document in 9 days what it typically takes 9 or more months to do yourself
THE “WHY” BEHIND PROCESS OPTIMIZER
Many organizations have no documented processes for their employees to follow and no Business Playbook. Others have some documentation, but the processes are not updated regularly and consistently followed. As a result, their outcomes are inconsistent, both customers and employees are frustrated, and profitability suffers.
Created by former PF Chang’s executive and Lean Expert Heidi Berger, together with a former Record-Holding EOS Implementer®, Process Optimizer® is a team of expert facilitators who will help your organization define, document and OPTIMIZE your Core Processes so you’ll have consistent outcomes, happy employees, delighted customers, and dramatically increased profitability.
WHAT OUR CLIENTS SAY
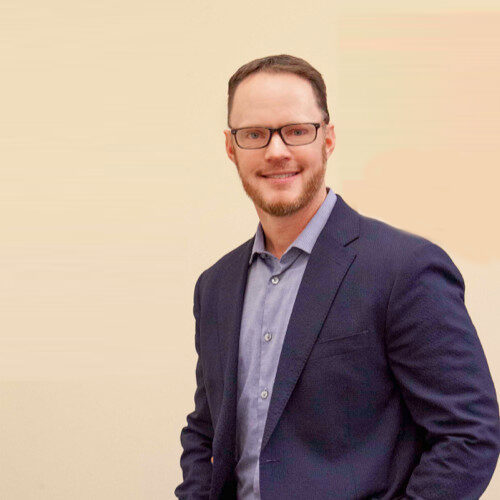
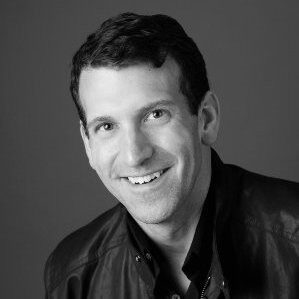
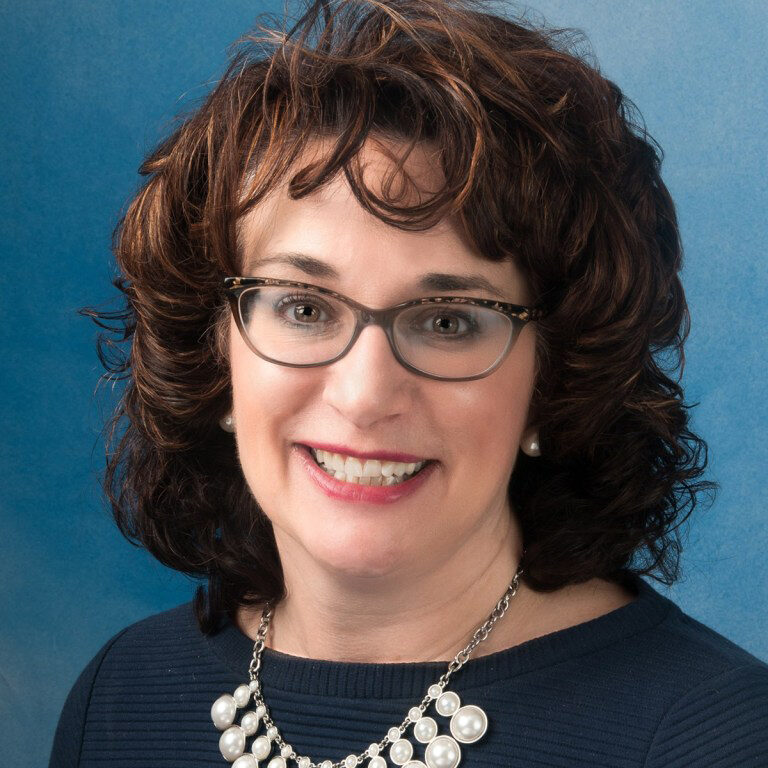
WHAT OUR CLIENTS SAY
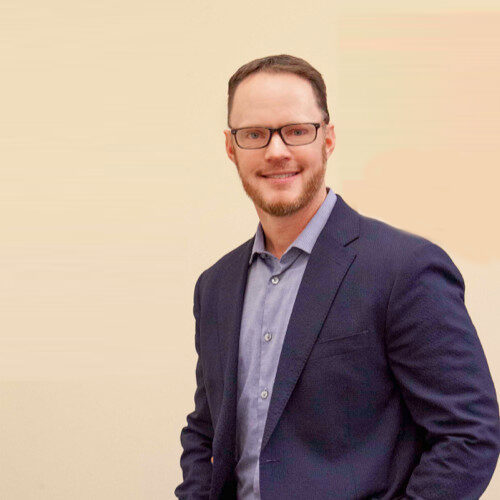
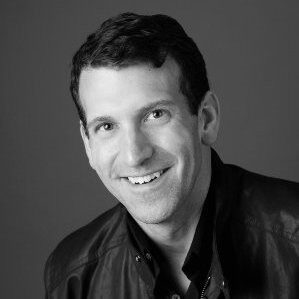
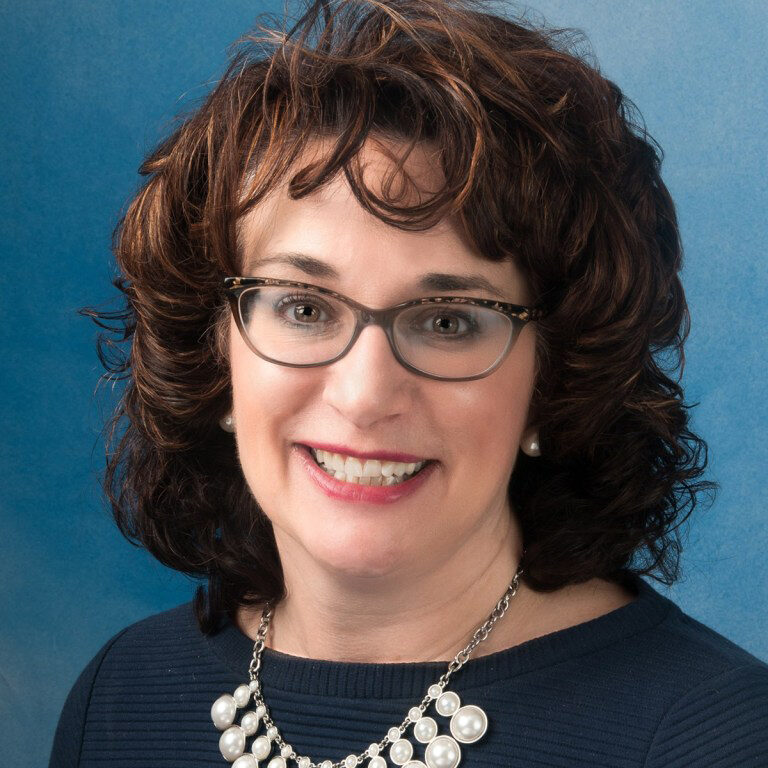
JUST A FEW OF THE COMPANIES WE’RE PROUD TO HAVE SERVED

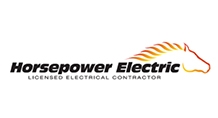
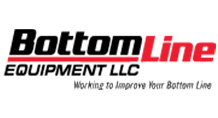
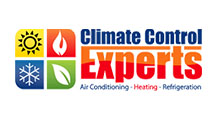
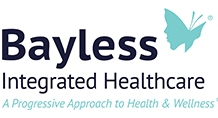
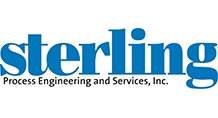
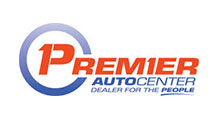
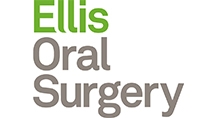
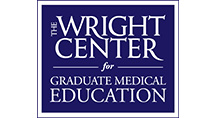
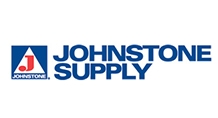
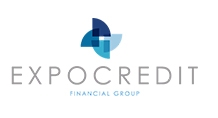
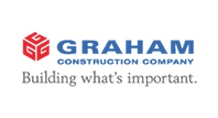
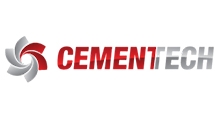
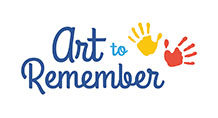
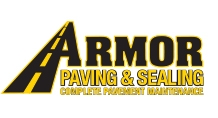
YOUR FRUSTRATION TO FREEDOM PLAN

BUILD YOUR BUSINESS PLAYBOOK
Design processes that make consistency, reliability and scalability a reality

GET EVERYONE ROWING IN THE SAME DIRECTION
Build teamwork, momentum and confidence

ENJOY YOUR FREEDOM
Feel confident knowing your business operates efficiently — even without you there
DISCOVER YOUR ORGANIZATION’S POTENTIAL
95% of organizational issues are related to processes and people. So if you lack an efficient way to document processes, your people will become liabilities. This scenario is not uncommon. It’s often hard for business owners to objectively see where inefficiencies disrupt workflow, paralyze growth and impact results. Complete this self-assessment and begin to uncover all your hidden deficiencies.